In our strive for standardization across the immersion cooling industry, we’ve joined forces with none other than Shell Lubricants (‘Shell’) to deliver a complete and all-encompassing fluid portfolio tailored to the needs of the market. After rigorous testing, we’re proud to announce that Shell’s fluids have been approved for use in Submer’s immersion cooling products.
As part of our testing journey, we compared Shell’s line of immersion cooling fluids with conventional immersion cooling fluids on the market and found an impressive improvement when it comes to fluid stability.
Improving Datacenter Performance: Why Measuring Stability Matters
Fluid stability refers to how long a fluid will last without requiring filtration, replacement, or topping up. It’s possible to enhance base fluid stability on a chemical level by using oxidation inhibitors as additives.
To evaluate the stability of Shell’s immersion cooling fluids, we used IEC 61125 accelerated oxidation method to predict fluid performance over time. The test exposes the fluid to a high temperature (120°C) and injects oxygen over 500 hours. The purpose of this test is to simulate 14 years of aging compared to typical immersion cooling temperatures (usually at a maximum of 60 °C). Although actual in-service performance typically deviates when exposed to server materials, this accelerated oxidative aging provides a reliable benchmark for comparison between fluids.
To quantify stability, two key parameters were taken into account: acidity and loss factor. While acidity often carries negative connotations related to corrosion, in this context acidity truly refers to the presence of trace acidic constituents or contaminants in the fluid, measured by Total Acid Number (TAN). These tend to affect the dielectric property of the fluid and are used as an indicator of when an oil needs replacement.
The loss factor, or dielectric dissipation factor (DDF), is a measurement of the conductive contaminants in the fluid. This factor is influenced by temperature and moisture levels and serves as a useful indicator of degradation or contamination. Since the dissipation factor indicates the efficiency of dielectric fluid to hold electricity or behave as an insulating fluid, a higher number points to decreased electrical resistivity, and therefore a lower number is most desirable.
Results of the Immersion Cooling Fluid Stability Testing
In summary, the accomplishments of the immersion fluid testing regarding stability were as follows:
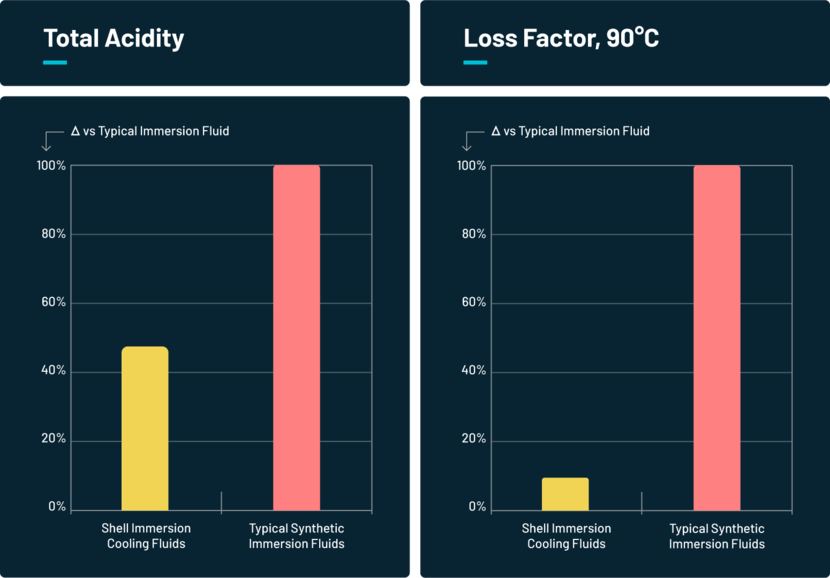
In Figure 1, we compare the total acidity at the end of the test for Shell immersion cooling fluids compared to typical synthetic immersion fluids. Lower acidity indicates less oxidation and less degradation, and here we can see that Shell immersion cooling fluids exhibited acidity levels of less than 50% of that of typical synthetic immersion cooling fluids.
In Figure 2, the loss factor at the end of the test of Shell immersion cooling fluids is compared to typical synthetic immersion fluids. A lower loss factor indicates less contamination and stronger dielectric properties. Shell immersion cooling fluids have demonstrated a loss factor of less than 10% than that of a typical immersion cooling fluid.
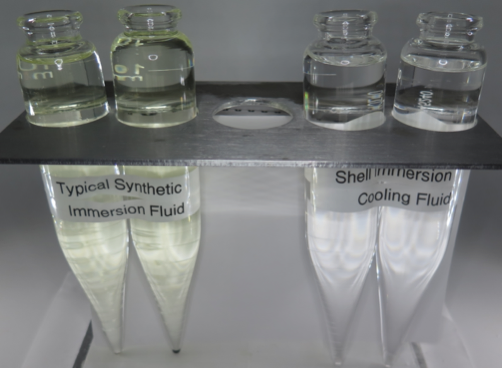
Key Takeaways
Shell immersion cooling fluids are more stable with improved oxidation stability properties over time than synthetic hydrocarbon immersion cooling fluids.
This collaboration with Shell has brought us fluids that exceed industry standards in terms of longevity. Our results have proven their effectiveness as a reliable, efficient and approved Shell immersion fluid solution for immersion cooling, and we are continuing to conduct further testing to align our offering with the evolving needs of the market.